News
Filtration efficiency, water consumption and ongoing maintenance costs are important factors to consider when selecting an industrial filtration system.
Industries across the manufacturing spectrum — whether producing beverages, dairy products, petroleum, chemicals, plastics or electricity, to name a few — generate heat as a byproduct of the manufacturing process. In most instances, the heat must be removed continuously from the production process to prevent equipment overheating. Removing the generated and excess heat also helps reduce cycle times for increased process efficiencies.
The two most commonly used mediums for heat rejection are air and water. The most effective and efficient cooling means employ both, which is why cooling towers are so prevalent across the industrial landscape. The cooling-loop water is exposed to atmosphere through nozzles in the cooling tower while air is forced across the water surface for evaporative cooling. The cooled water is recirculated back to the manufacturing process.
Unfortunately, the very nature of cooling tower operation introduces airborne particulate such as pollen, dust and other organic debris to the cooling-water loop. If left unchecked, these contaminants will reduce heat transfer efficiency and, by extension, reduce process efficiencies and increase operating costs. Fouled heat exchangers and plugged nozzles often are to blame for production slowdowns or, worse, production downtime. Water is the lifeblood of the cooling system, and contaminated water can be the cooling system’s death knell.
Two primary components of maintaining healthy cooling water are water treatment and filtration. A typical water treatment regimen consists of pathogen control, scale and corrosion prevention, total dissolved solids control and pH adjustment. Water treatment works most effectively in the absence of suspended particulate contaminants. This is why professionals engaged in water treatment either employ or recommend filtration to remove the harmful contaminants.
Filtration systems fall into two broad categories: manual and automatic (self-cleaning). The following is a discussion of the most common types of filtration technologies for process cooling water, along with the pros and cons of each.
Manual Filters
On the positive side, a manual filter produces no waste stream or backwash. If local authorities have a zero-discharge regulation with respect to production wastewater disposal, or if a sanitary drain is otherwise unavailable to the filter, a manual filter would be a good choice. Manual filters have a lower capital cost compared to automatic filters.
As the name implies, however, manual filters require periodic manual replacement or cleaning of the filter element. In keeping with today’s green mindset (and the aim of reducing long-term costs of ownership), manual filters with a cleanable, reusable filter element are preferred over single-use, disposable elements. Examples of reusable filter elements include perforated or mesh screens, and disc element filters. Disposable filter elements include melt-blown, string-wound and pleated paper cartridges. Other disposable types include cloth or polymeric filter bags.
A hybrid filter consists of a conical stainless-steel screen contained within a stainless-steel housing. Unfiltered water enters into the open screen bottom, and particulate are captured on the screen interior. Any heavy particles settle to the bottom of the housing’s solids-collection chamber.
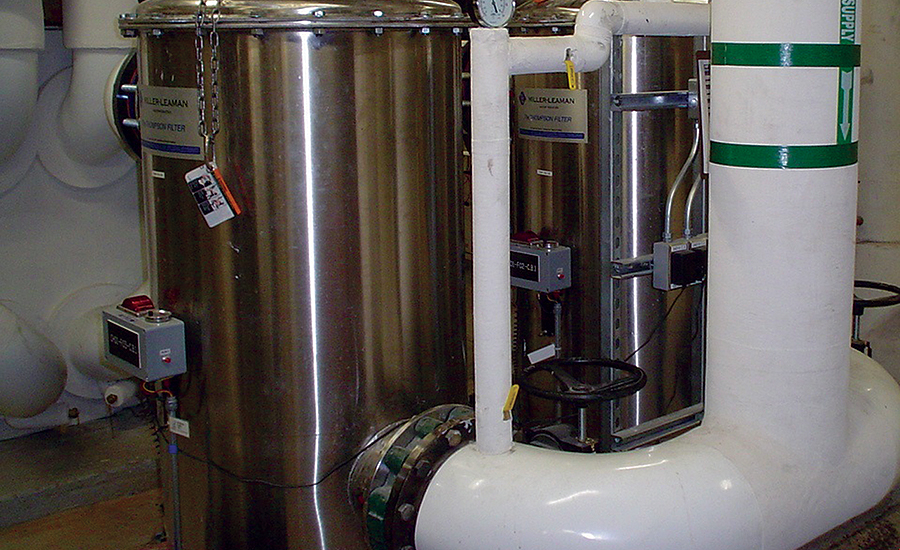
Hybrid Filters
Hybrid filters falls between the manual and automatic filter categories. A typical hybrid filter consists of a conical, stainless-steel screen contained within a stainless-steel housing. Unlike a conventional screen filter with the screen open at the top and closed at the bottom, the hybrid screen is the opposite: the top is closed and the bottom is open. Unfiltered water enters into the open screen bottom, and particulate are captured on the screen interior. Any heavy particles settle to the bottom of the housing’s solids-collection chamber, where they can be purged to a drain through a bottom purge outlet. The purge is accomplished with either a manually or automatically operated ball valve.
With no moving parts, the hybrid design is reliable. A low pressure drop is inherent to the design: less than 1 psi (clean) at maximum design flow rate. As would be expected, capital cost is lower than a fully automatic filter, making hybrid filters a good choice for side-stream and full-stream applications. In addition, the footprint is the smallest of all filter technologies discussed in this article.
In hybrid filters, all of the components are stainless steel construction. A range of screen mesh sizes allows a customized fit to specific applications. The inverted screen allows heavy particulate to settle in the lower solids-collection chamber, reducing screen-maintenance frequency.
However, while maintenance frequency (screen cleaning) is reduced, it still requires periodic cleaning. A differential pressure alarm can alert to this condition.
While maintenance frequency (screen cleaning) is reduced with hybrid filters, they still require periodic cleaning. A differential pressure alarm can alert to this condition.
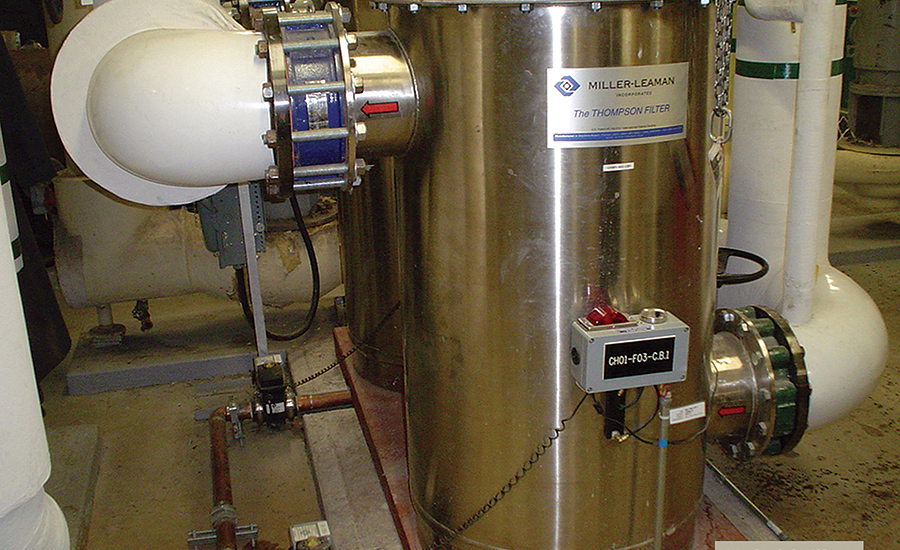
Automatic Filters
Popular automatic filter technologies include sand filters, disc filters and centrifugal separators. The primary positive benefit is obvious: These filters do not require routine maintenance. The primary negative concern is cost. These filter types are more expensive than manual, non-self-cleaning filters.
Sand Filters. A typical sand filter system consists of the sand filter, a pump and control panel, factory installed on a skid for ease of field placement. Sand filters require little regular maintenance and can filter down to approximately 10 to 15 microns using conventional silica quartz sand. Ultrafine granular media is claimed by some manufacturers to remove particulate down to 0.5 micron.
There is a drawback to using ultrafine media, however. Sand filters using ultrafine sand must backwash at a lower-than-normal flow rate (typically only 10 gallons per minute per square foot of filter surface area) to prevent ultrafine sand loss. This translates to 0.25” per second upflow velocity to remove contaminants from the sand bed. Some contaminants remain and accumulate over a short time, causing increased filter backwash frequency and even greater water consumption.
Sand filters have a high backwash flow rate and often require a surge tank, which fills quickly during a backwash cycle and allows the wastewater to flow at a slower rate to accommodate a floor drain. Sand filters consume a high quantity of water during the backwash cycle relative to other self-cleaning filter technologies. Another layer of complexity is added with level controls in the surge tank to prevent accidental overflow.
Other drawbacks can include the time required and expense of media replacement and disposal. In addition, crystalline silica is classified as a human lung carcinogen, so appropriate safely measures should be taken when handling the filter media. The cavity below the filter underdrain is essentially stagnant during filtration, creating a potential breeding ground for bacteria. Bacteria also breed in the sand bed. (That is the unpleasant odor experienced when changing the media.)
Centrifugal Separators. A typical centrifugal separator filter system consists of the centrifugal separator, a pump and a pump motor control panel. The components are factory installed on a skid. As the name implies, centrifugal separators rely on centrifugal force to separate particulate from cooling tower system water.
Centrifugal packages are lower cost than other automatic filter technologies. With no moving parts in the separator, centrifugal separators have the simplest means for extracting large, heavy particulate from water.
By nature, airborne particulate are very light and fine. As the primary contaminant in the system water, the particulate’s specific gravity is close to that of water. (Otherwise, it would not be in suspension.) For this reason, centrifugal separators are not as efficient as other automatic filters at removing particulate; instead, centrifugal separators are only marginally effective at removing them.
To achieve fine filtration, many centrifugal separator, pump and skid packages include a bag or cartridge filter (sometimes called a solids-recovery vessel). In this design, a small percentage of the separator flow is directed into the bag or cartridge filter. The filter bag and cartridge require frequent replacement and consequently, the filter system is no longer fully automatic or self-cleaning.
Unlike a conventional screen filter with the screen open at the top and closed at the bottom, the hybrid screen is the opposite: the top is closed and the bottom is open. Unfiltered water enters into the open screen bottom, and particulate are captured on the screen interior.
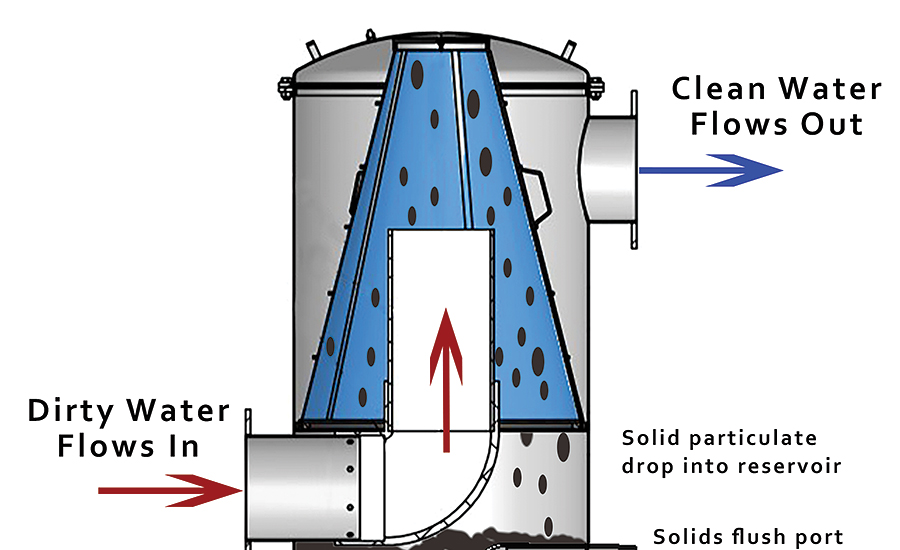
Disc Filters. Disc filter media consists of thin polypropylene discs with fine, angled micro-grooves on both sides of each disc. The discs are stacked on a spine and held in compression with a spring-loaded top cap. The assembly is contained within a pod. Each pod is capable of handling flows up to 130 gallons per minute. Higher flows are accommodated by adding pods. When placed on top of one another, this creates a series of intersections where fine waterborne particulate are captured. The contaminants are removed by reversing flow through the spines in sequence during the self-cleaning cycle.
Disc filters consume considerably less water than sand filters during the self-cleaning cycle. For example, a 300 gallons per minute disc filter will consume 35 gallons while a sand filter at the same capacity will consume 900 gallons. In most applications, the disc filter backwash flow rate is only 45 gallons per minute, making a surge tank unnecessary.
In disc filters, the pods backwash in sequence. Also, filtration is continuous during the self-cleaning cycle, which is orders-of-magnitude more aggressive when compared to a sand filter. This helps ensure removal of all accumulated contaminants in the disc media. Disc filters do not have any stagnant areas for bacterial growth, and the polypropylene disc media life typically ranges between 10 to 15 years. Replacement is quick and straightforward.
However, polymeric components in a disc filter limit the maximum operating temperature to 125°F (52°C), making this an unsuitable filter for circulating loops operating at elevated temperatures. Maximum operating pressure is also limited to 125 psig.
In conclusion, filtration efficiency, water consumption and ongoing maintenance costs are important considerations in selecting the most appropriate filtration system for any given application.